In today's rapid manufacturing landscape, the capability to swiftly launch products to market is more critical than at any time in the past. Businesses are constantly searching for creative methods to enhance their production processes while upholding high standards. One technology that has surfaced as a breakthrough in this area is accelerated injection molding. This technique not only speeds up the manufacturing schedule but also offers a level of precision and flexibility that can notably enhance product development.
Rapid injection molding transforms the conventional methods of production by cutting lead times and lowering costs associated with tooling and material usage. By employing cutting-edge techniques and technologies, manufacturers can create high-quality prototypes and final products in a fraction of the time typically required. This agile approach not only meets the demands of a competitive industry but also enables businesses to respond swiftly to customer input and evolving trends. As companies continue to leverage the speed of rapid injection molding , they are setting themselves up for success in an always evolving economic environment.
Comprehending Accelerated Injecting Forming
Fast injecting molding is a production process that considerably hastens the production of plastic parts. This technique entails developing molds in a quick and affordable manner, allowing for effective mass manufacturing. In contrast to conventional injecting molding, which can take weeks for shape creation, accelerated injection molding cuts this time to just a few days. This swiftness is essential for fields aiming to introduce their products to market swiftly while upholding high standards and precision.
The technique typically uses innovative materials and technologies to simplify shape development. By employing techniques such as additive manufacturing or CNC fabrication, companies can develop prototypes and manufacturing molds that fulfill exact specifications. This not only enhances the turnaround period but also facilitates for quick revisions during the development phase, allowing organizations to adapt their goods based on consumer input or shifting demands without incurring significant delays.
Additionally, rapid injecting molding supports a spectrum of production needs, from low-volume runs to big series production. It is particularly helpful for startups and firms debuting new products, as it cuts the upfront expenses and risks linked to conventional production methods. The flexibility and effectiveness of accelerated injection forming place it as a critical factor in modern goods innovation strategies, empowering firms to innovate and compete effectively in the current rapid market.
Benefits of Rapid Injection Molding
Rapid injection molding offers a considerable boost in production speed when set against traditional methods. By employing advanced technology and materials, manufacturers can create molds quickly, allowing for a quicker turnaround time from concept to production. This speed allows companies to respond more efficiently to market demands and launch new products within compressed time frames, offering them a competitive edge.
Cost-effectiveness is another significant plus of accelerated injection molding. While the initial investment in tooling may still be considerable, the ability to produce high volumes of parts in a reduced time markedly lowers the overall manufacturing costs. Additionally, lowered labor and overhead expenses during the production process contribute to increased profitability, making it a feasible option for various industries aiming to optimize their manufacturing operations.
The versatility of fast injection molding is also a noteworthy merit. This technique allows for quick design iterations and modifications, allowing companies to test and improve their products without significant delays. As a result, businesses can innovate more openly and adapt their designs based on real-time feedback, ensuring that the final products meet customer needs and market expectations effectively.
Implementations and Examples
Fast injection molding plays a essential role in multiple industries, notably in retail products, vehicle manufacturing, and medical devices. In the consumer goods sector, companies use fast injection molding to produce prototypes and final parts quickly. This rapidity not only reduces time to market but also allows brands to adapt to changing market demands more swiftly, ensuring that they remain in the game. For instance, a top toy manufacturer employed fast injection molding to create new product lines in reaction to seasonal trends, resulting in a significant boost in sales.
The automotive has also embraced fast injection molding for its ability to create components with complex designs and exactness. A notable case featured an automotive manufacturer that used fast injection molding to produce detailed interior parts with improved resilience and lightweight features. By streamlining the production process, the company was able to cut development time by multiple months, leading to quicker assembly and fewer delays in bringing their new vehicle models to dealerships.
In the medical field, fast injection molding has changed the way medical devices are created and made. A case study of a medical device company illustrates how they utilized this technology to produce customized surgical instruments. The rapid prototyping capabilities allowed them to test multiple designs expeditiously, eventually landing on the best version for their needs. This not only augmented their product range but also boosted patient outcomes by ensuring that the instruments were precisely crafted for precision and effectiveness in surgical procedures.
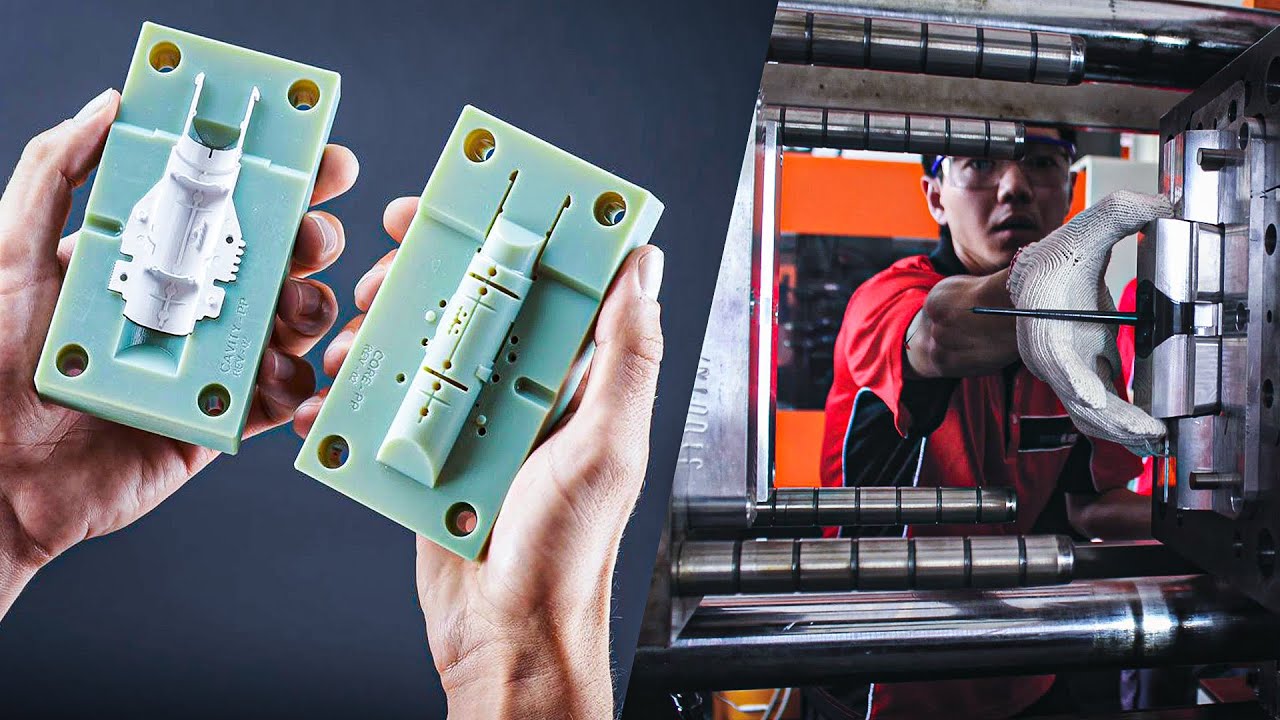